PT. Petrosea Tbk; 9 Positions
Posting date: February 13, 2020 Expiry date: February 27, 2020
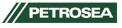
PT Petrosea Tbk. is a multi-disciplinary mining, infrastructure and oil & gas services Company with a track record of achievement in Indonesia since 1972. We offer a competitive advantage through our ability to provide complete pit-to-port mining solutions, integrated engineering and construction capabilities as well as logistic support, whilst demonstrating absolute commitment to health, safety & environment, quality management, and business integrity.
We also provide services for the oil and gas industry in Indonesia through our Petrosea Offshore Supply Base (POSB) deep-water supply base that consistently delivers international standard and cost-effective services to all of our clients. Petrosea has been listed on the Indonesia Stock Exchange (IDX: PTRO) since 1990 and was the first publicly listed Indonesian engineering and construction Company in Indonesia.
We are currently taking applicants for the following position:
SENIOR CONTINUOUS IMPROVEMENT ENGINEER
(Assignment: Head Office)
Actively contribute in Equipment KPI review and Best Practice project initiatives; Monitor Asset performance, analyze multivariate data, provide technical support which related (but not limited) to Maintenance Strategy/ system, Machine Application, Equipment Selection/ Modification, in order to initiate achievable Improvements Initiatives and Equipment Reliability within Asset Management Group.
Requirements:
• Min. S1 degree in Civil / Mechanical / Industrial Engineering with 3-5 years experiences in Mobile and Plant Maintenance in Mining Industry
• Has proven knowledge in CI tool for Best Practice Management (6sigma, RCM, FMEA, Kaizen, etc.)
• Has extended knowledge of Heavy Equipment Maintenance Management
• Has extended experience in Equipment Health and Machine Application tools (SOS, TPMS, VIMS, ET, FPO, VHMS, INSITE, MIC, etc.)
• Proficient in analysing multivariate technical data resources and generating technical reports
• Has good knowledge in analysis of costs on improvement and modification projects
• Highly competent computer skill in Microsoft environment (incl. Word, Excel, PowerPoint, and Access)
• Is highly competent in managing reports for regular and management review; action plan presentation
• Fluent in English, both oral and written
• Willing to travel to project sites in remote locations
Responsibilities:
• Support HSE programs and the Environmental management system to ensure the effectiveness of the programs conform to official standards and requirements.
• Manage and control Asset Management POAP to ensure compliance between Maintenance Strategy Initiatives/ plans and Implementation, in order to close the gaps as per agreed targets.
• Manage and provide control over CI projects engaged across Asset Management functions to ensure achievements are within target set by the process owners (time line, budget, resources, etc).
• Provide multivariate technical data analysis from various resources using available CI Tool concepts (6Sigma, RCM, FMEA, Kaizen, etc.)
• Provide technical assistance in system development related to CI and align with engineering designs and drawings of any modification on facilities and equipment.
• Contribute in regular meetings with OEM Vendors and Industry Network Peers to keep up to date with the latest information and possible initiatives for asset reliability and cost saving projects, as well as to establish better CI culture within the company.
SENIOR PLANNER
(Assignment: Head Office)
Plan, coordinate, schedule and monitor all maintenance activities in >6 months horizon pertaining to asset project (heavy equipment) in order to ensure all maintenance activities in project are effective and efficient in timely manner conform to the project schedule and budget.
Requirements:
• Min. Education & experience:
- Min S1 Engineering with 7 years’ experience in heavy equipment Mtc operation & Planning, or
- Min D3 Engineering (preferably Mechanical) with 10 years’ experience in heavy equipment Mtc operation & Planning, or
- Min STM Mechanical with 15 years’ experience in heavy equipment Mtc operation and Mtc Planning
• Experience / familiar in using CMMS (Computerised Maintenance Management System) Program
• Strong knowledge and concept for setting up Preventive Maintenance
• Preferably to have on-hand experience in :
- Work Planning and Scheduling
- Maintenance Budgeting/Planning Cost
- Maintenance Data and Task Analysis (Oil Analysis, Condition Monitoring, RCM, Reliability)
• Excellent computer skill
• Able to work in detail, time management, target oriented, good reporting system
• Able to show and maintain good attitude, open, honest, proactive and respecting other
• Willing to work in Jakarta with extensive travel to project/sites in remote areas
• Internal candidate (existing employee) with lower education background may be considered if having some proven experience
Responsibilities:
• Provide long term maintenance planning (>3 months) applied to all company asset (or at the moment is applied on heavy equipment in the company for Mining operation), release on time as per schedule complete with parts/component schedule and its budgeted cost/spend.
• Coordinate with Maintenance (Mtc) Planning Superintendent, Mtc Planning Coordinator and Component Planning Coordinator to develop Long term (>3 months) maintenance planning schedules for multi purposes resources planning e.g. budgeting, parts & component planning, man power and tooling planning.
• Coordinate with User (e.g. Mining) Engineering team (e.g. Mine Engineering Supt or Senior Mining Engineer) to build robust approach in preparing long term maintenance planning.
• Coordinate with Asset Finance team in providing long term maintenance budgeting and meeting Corporate Finance need on finance-related forecasted data/cost in regard with Mtc operation.
• Coordinate with Mtc System & Strategy section to identify and check the integrity of data, approach and current system capability to produce robust long term Mtc plan.
• Prepare and monitor the implementation of Shutdown planning in order to increase the plan accuracy and to ensure all resources and materials are on hand when required.
• Check and investigate all variances from target and report to Planning Manager in order to maintain data accuracy and improving the robustness of the approach in building-up the Long term Mtc plan.
• Analyze in general the historical event/cost and provide information to Asset Engineering team on likely event to adjust based on data/fact.
• Originate, monitor and control requests for parts and resources in order to ensure they are available when required and without contributing to “overstock” and unnecessary storage of parts.
• Support and advise Inventory Controller regarding to stock level availability in order to determine accurate minimum and maximum stock levels.
• Maintaining and implementing HSE programs including Environmental Management System to ensure the effectiveness of the programs conform to official standard and requirements.
BUSINESS SOLUTION SUPERINTENDENT (ASSET MANAGEMENT)
(Assignment: Head Office)
Plan, coordinate, and supervise all activities related to the design, development, implementation, maintain, support and upgrade of asset management information systems and software applications. The Business Solution Superintendent is also responsible to periodically review the System/ERP to ensure system process and applications remain relevant to the maintenance strategy. Initiate the changes required
Requirements:
• Education & experience:
- Bachelor Degree in Engineering in any discipline is preferred with minimum 8 yrs experiences in heavy/mobile equipment Maintenance Management or
- Min D3 Engineering (preferably Mechanical) with 12 yrs experiences in heavy/mobile equipment Maintenance Management or
- Min STM Mechanical/High School with 16 yrs experiences in heavy/mobile equipment Maintenance Management
• Excellent understanding of the organization’s goals and objectives.
• Strong knowledge of system and software of CMMS and Direct, hands-on experience with (Computerised Maintenance Management System), ERP Program, CM Database, SAP-PM most preferred.
• Strong knowledge & concept for set-up Preventive Mtc, additional know-how in Predictive Mtc is a plus.
• Experienced with Asset and maintenance Key Performance Indicator Measurement and Analysis.
• Knowledge of database design and file management techniques.
• Strong customer-service orientation.
• Excellent written and oral communication skills.
• Excellent listening and interpersonal skills, Ability to communicate ideas in both technical and user-friendly language.
• Highly self-motivated and directed.
• Keen attention to detail.
• Able to prioritize and execute tasks in a high-pressure environment.
• Experience working in a team-oriented, collaborative environment
• Willing to travel in any location e.g. any project/site location which in remote areas.
Responsibilities:
• Support HSE programs and environmental management system to ensure the programs conform to quality standards, and statutory and regulatory requirements.
• Establishing Master Plan and Road Mapping of Asset Management for Business Solution and Design Definition.
• Ensuring necessary system updates & supports required for efficient maintenance management, are well coordinated & implemented
• Ensure to maintain the CMMS/ ERP framework & database system projects necessary for managing maintenance functions at all functions within Asset Group.
• Ensure that continuous improvement plan for ERP/CMMS/ Asset Portal are executed with regular discussion with ICT
• Developing plan for CMMS/ERP continuous improvement – provide decision & direction on smooth transition on any system up gradation/ enhancement within asset group
• Review and make sure that business process updated, maintaining and alignment with the asset management operation and supported by system (ERP) and other legacy system.
• Communication and socialization to Asset Management Personnel and end user for any changes and new update for CMMS / ERP specially related with Asset Management Operation.
• Coordinate with ICT / ERP Support, system engineering to ensure ICT - AMG initiatives can be completed on time as target.
• Coordination with ICT on regular basis on the system shortfalls and ensuring for timely implementation of the recommended actions.
• Active involvement on Asset management procedures – policies review & development
• Proactive involvement in other key leadership role as assigned by supervisor.
• Performing assessment, analysis of the asset management business process, system in order to provide efficient and effective of asset management business and operation.
• Mentor & develop people within asset group in system & planning functionality.
FABRICATION ENGINEER
(Assignment: Balikpapan Office)
Fabrication activities incl. plan, coordinate, Technical Documentation for steel structure material requirement and carry out technical evaluations including studies and calculation for steel structure for fabrication. Provide a safe, Reliable and Effective production in machining/Fabrication and Liaise with supervisor for and possible improvement/solutions. Provides manufacturing decision-making information by calculating production, labour, and material costs; reviewing production schedules; estimating future requirements And to ensure that all Fabrication Process can be effective and efficient on time according to time and budget.
Requirements:
• Minimum Bachelor degree in Mechanical Engineering
• Minimum 5 (five) years experiences in Welding/Fabrication in mining industry
• Proactive safety attitude
• Ability to evaluate technical and Economic factor, recommending engineering and manufacturing action for attainment of design objective of process or product by applying knowledge of material science and related technologies
• Experience/familiar in using CMMS (Computerized Maintenance Management System) Program
• Strong knowledge and concepts for the Fabrication Workshop process that is organized to create designs and drawings that are safe for fabrication and can be operated on site
• Preferably to have on-hand experiences in:
- Design and Drawing (AUTO CAD)
- Calculation for steel structure for Fabrication
• Excellent computer skill, medium English capability (both passive & active)
• Able to work in detail, time management, target oriented, and good reporting system
• Able to show and maintain good attitude, open, honest, proactive, and respecting others
• Willing to work in any location e.g. any project/site location which in remote areas.
Responsibilities:
• To manage, review and implement all Fabrication Plan incl. all requirement (Material selection, Calculation design, tools list Requirement, scope of work/activity list, job duration, trade, number of trade and to some extent –estimate cost
• To manage all inspection sheet Inspection Fabrication include NDT inspection, Volume matric, SWL (Safety Working Limit), WLL (Work Load Limit) with coordination Lifting Department.
• To evaluate and analyse post-Maintenance plan data, e.g.:
- Evaluate feedback document of Fabrication plan jobs (Drawing)
PDM INTERPRETER
(Assignment: Balikpapan Office)
To enable multivariate analysis of all machine health parameters and determine criticality of components based on available system within the company, and prioritize corrective maintenance actions & recommendations through to maintenance execution team in timely manner; as well as to gather feedbacks from maintenance execution team to improve corrective maintenance actions & recommendation going forward.
Requirements:
• Minimum S1 Degree in Mechanical/Civil/Industrial Engineering, and/or Minimum 5 years of experience in Mobile Plant Mining Industry & Asset Equipment Health initiatives (with minimum experience 5 years in field)
• Advanced knowledge in maintenance analytical tools (VIMS, VHMS, ET, Mpro, Insite, NDT, Thermal analysis, etc.)
• Advanced knowledge in mechanical awareness
• Multivariate data analytical capability
• High experience in fatigue & failure analysis
• Advanced understanding of heavy equipment maintenance management
• High experience in fluid analysis (oil, coolant, fuel, grease, fire suppression system)
• Advanced understanding of heavy equip/machine application analysis
• Advanced computer literacy (Ms. Excel, Ms. Access, MS. Power Point, ERP)
• Proficient lateral & analytical thinking/skills
• High experience with maintenance work flow management
• High experience with maintenance KPIs & work management compliances
• Deep understanding of maintenance workforce roles & responsibilities
• Deep understanding of supply chain work flow
• High communication skills
• Willing to travel to project sites in remote locations
• Fluent in English, both oral and written.
Responsibilities:
• Daily monitor critical components
• Assign critical components action based on priority
• Validate default recommendation from system
• Give recommendation action for investigation
• Give recommendation reference for component repair/ replace
• Ensure WO schedule plan as per priority (with Planning team)
• Ensure WO execution as scheduled (daily with Executor team)
• Ensure quality check on all recommendation action performed
• Communicate with SME (Subject Matter Expert) team related to specific field influences (i.e.: fuel quality, haul road condition), for refining recommendation
• Tyre management with strength command and instruction style
• Create and Close Work Order on SAP system
• Open PdM Dashboard web, include input and report
• Open Oil Commander web for Petrosea all sites and download data SOS
Quality Controller (Fabrication)
(Assignment – Balikpapan)
Provide a safe, reliable & effective production in machining / fabrication and liaise with Superintendent/Supervisor for any possible improvements / solutions. Conduct quality assessment to PTP and or approved specification standards
Requirements:
• Minimum Bachelor Degree in Mechanical Engineering, or any relate discipline
• Min. 5 year experiences in a Construction QC and Fabrication,
• Strong understanding of quality control standards and testing techniques.
• Understanding of fabrication requirements and production targets.
• Ability to review samples, drawings or instructions to understand specifications of output
• Ability to evaluates technical and economic factors, recommending engineering and manufacturing actions for attainment of design objectives of process or product by applying knowledge of quality control science and related technologies
• Understand Failure analysis special Steels & Fabrication Rework & Redo
• Qualifications and supporting certificates in field of trade / required duties.
Responsibilities:
• Strong safety awareness at all times and adheres to Petrosea guidelines and regulations. Lead by good example in this area and show high standards of commitment to safety and surrounding environment. Always use all correct PPE and LOTO procedures
• Perform regular quality assessments on all incoming materials to fabricate and outgoing products and also to ensure compliance to all fabrication procedure and timeframe.
• Reject all products and materials that fail to meet quality expectations.
• Measure product dimensions, examine functionality and compare the final product to the specifications.
• Recommend improvements to production process to ensure quality control.
• Teach the production team about quality control concern to improve product excellence.
• Resolve quality-related issues in a timely manner. (Include Investigate any Rework/Redo Job)
• Generate and distribute QC report periodically.
Quality Controller (Rebuild Component)
(Assignment – Balikpapan)
Provide a safe, reliable & effective production in machining / fabrication and liaise with Superintendent/Supervisor for any possible improvements / solutions. Conduct quality assessment to PTP and or approved specification standards
Requirements:
• Minimum Bachelor Degree in Mechanical Engineering, or any relate discipline
• Min. 5 year experiences in a Construction QC and component rebuild or Remanufacturing,
• Strong understanding of quality control standards and testing techniques.
• Understanding of component rebuilds requirements and production targets.
• Ability to review condition of component core, detail measurement result and disassembly/assembly instructions to understand specifications of output
• Ability to evaluates technical and economic factors, recommending re-usable part/salvage guidance and manufacturing actions for attainment of component function by applying knowledge of quality control science and related technologiesQualifications and supporting certificates in field of trade / required duties.
Responsibilities:
• Strong safety awareness at all times and adheres to Petrosea guidelines and regulations. Lead by good example in this area and show high standards of commitment to safety and surrounding environment. Always use all correct PPE and LOTO procedures
• Perform regular quality assessments on all incoming component cores to rebuild and outgoing products and also to ensure compliance to all rebuild procedure and timeframe.
• Reject all parts and materials that fail to meet quality expectations.
• Examine functionality and compare the final product to the specifications.
• Recommend improvements to production process to ensure quality control.
• Teach the production team about quality control concern to improve product excellence.
• Resolve quality-related issues in a timely manner.
• Generate and distribute QC report periodically.
• Team work and communication within all Petrosea work areas.
• Notify your immediate supervisor if any unsafe equipment, tooling or incident.
SENIOR DOCUMENT CONTROLLER
(Assignment: Head Office)
Monitor and control Engineering, Construction, and Project Management documentation in order to ensure all documents are well manage and conform to Engineering and Quality procedures.
Requirements:
• Minimum Diploma Degree in any major
• Min. 5 years experiences as document controller
• Able to used computer program
• May be required to work extended hours to meet reporting deadlines
• May be required to travel to site
Responsibilities:
• Monitor the implementation of document control procedures to ensure all documents circulations are conform to company’s procedures
• Train others in the use of standard document control database software in order to provide support to the users
• Provides training and guidance to subordinates; Leading a team of document controllers
• Coordinate and liaise with project, procurement and design staff on document control issues in order to update issues and system in document control
• Monitor and supervision of document control center to ensure document control center are well manage
• Update and implement the latest knowledge to ensure the Engineering library is maintained to latest revisions
• Support projects, external parties, Engineering & Construction team by ensuring that all documentation on projects are properly distributed, catalogued, and filed for easy retrieval
• Ensure that all documents are registered and controlled in the system database software
• Ensure document management objectives are clearly understood and followed in accordance with in the job function
• Review incoming engineering drawing packages to ensure all required documents and drawings are received
• Ensure external engineering client follow the standard, procedures work instruction, and specifications
• Providing guidance / resolving issues related to project documentation through the progress of the project until close-out
• Managing internal and external users to the in-house web based document collaboration system and dealing with queries and complaints
• Communicates, monitors, and assesses the conformance of documentation to the document management protocol
• Assists in the establishment, development and achievements of departmental documentation management committees
• Maintain and implementing HSE programs including Environmental Management System to ensure the effectiveness of the programs conform to official standard and requirements.
PROCUREMENT MANAGER
(Assignment: Head Office)
Direct and control the procurement function activities in order to ensure efficient and economical operation of the department, conforming to the established goals and objectives to accomplish corporate profit, growth and investment return as well as procedural compliance and commercial accountability.
Requirements:
• Minimum Bachelor degree in any disciplines
• Minimum 10 years of related experiences preferably in Mining, Construction or Oil and Gas company
• Able to work under pressure and develop and maintain effective purchasing control mechanism
• Able to prepare, justify and administer a budget
• Able to administer contract management
• Able to establish policies and procedures and evaluate program effectiveness.
Responsibilities:
• Develop and maintain procurement strategy for the department to ensure best value is achieved for the short to long terms for company, whilst it ensures surety of supply and develops strong partner type relationships with key suppliers
• Analyze & monitoring procurement activities starting with the forecasting & managing supplier database in order to achieve company operations effectively and efficiently
• Coordinate and negotiate framework for Preferred Vendor Agreements (PVA) & Capex to ensure the majority of spend is conducted under this framework
• Managing contract creation, execution, and analysis for the purpose of maximizing financial and operational performance and minimizing risk
• Develop and maintain supplier appraisal techniques and continually conduct supplier rationalization programs to ensure supplier overall performance
• Develop process operational plans in generate contract and service order in order to support organization business performance
• Establish Procurement policy, procedures and standards that are complied with the industry standards and regulations in order to support company’s operations effectively and efficiently
• Monitor and review local business initiative and aligning the implementation with user (business line) to develop the business migration program
• Develop and maintain a formal system for vendor/contractor rating and conduct regular vendor/contractor assessments to ensure data updated
• Monitor and liaise with internal and external audit to ensure that audit in the procurement function are conducted in a regular and timely manner and that any NCR’s are efficiently closed out
• Lead, coach and manage subordinate including recruitment and provide a proper development plan for them in order to maintain subordinate in attract, motive and retain.
If you are interested into applying this position, please register yourself at our online recruitment system, Petrosea Career (http://career.petrosea.com) and apply to position with title, not later than 26 February 2020.
Please be aware of certain frauds or misinformation regarding recruitment advertising on behalf of Petrosea. We never ask for any payments whatsoever from applicants or candidates during the recruitment process. We never ask applicants or candidates to use specific travel agent services to make arrangements for transportation and accommodation during the recruitment process.